· 4 min read
With embodied carbon being a key discussion point in construction recently, demand for low carbon building materials is increasing. Concrete gets a bad rep in these discussions due to the high emissions associated with it. However, it’s difficult to imagine a world where concrete is not used at all, and therefore the industry has made significant investments to develop lower-carbon concretes.
But what is low carbon concrete and how can it be adopted at scale to help the industry remain within planetary boundaries?
In this post we address the following questions:
- How is concrete made today?
- Why does traditional concrete have such a high footprint?
- What is low carbon concrete?
- How is low carbon concrete made?
- Are all low carbon concretes equal?
How is concrete made today?
In its simplest form, concrete is a mixture of paste and aggregates, or rocks. The paste, composed of cement and water, coats the surface of the fine (small) and coarse (larger) aggregates. Through a chemical reaction called hydration, the paste hardens and gains strength to form the rock-like mass known as concrete.
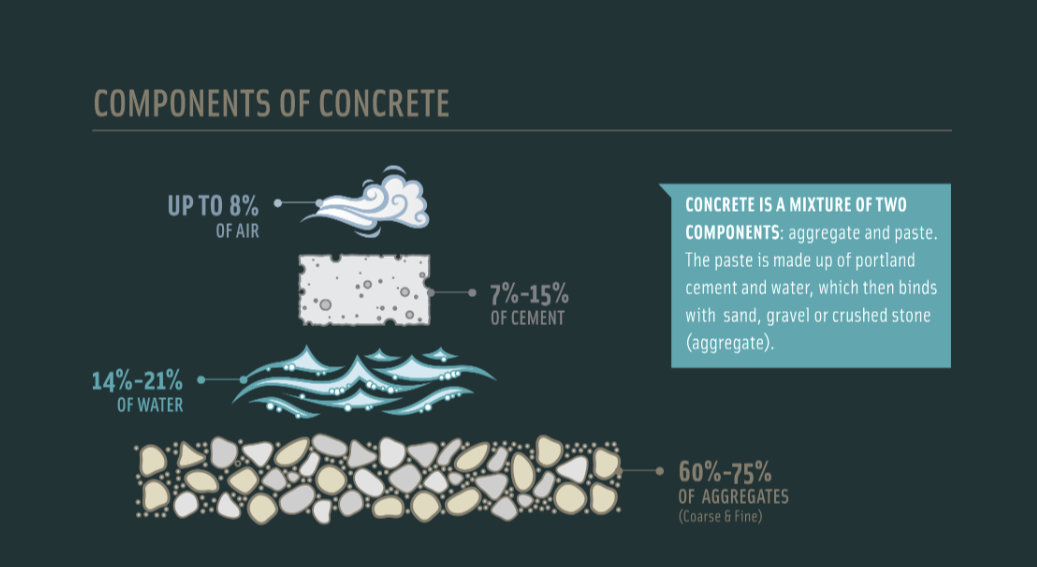
Why does traditional concrete have such a high footprint?
One reason why the carbon emissions are so high is because cement has to be heated to very high temperatures in order for clinker to form. A major culprit of this is alite (Ca3SiO5), a mineral in concrete that cures within hours of pouring and is therefore responsible for much of its initial strength.
What is low carbon concrete?
Low carbon concrete is concrete produced with a lower carbon footprint than traditional content. Other than a reduced carbon footprint, low carbon concrete should behave identically to its high carbon counterpart.
To create low carbon concrete, producers can implement a series of relatively low-impact changes to their production processes and mix designs.
How is low carbon concrete made?
To create low carbon concrete, producers can implement a series of relatively low-impact changes to their production processes and mix designs.
There are 3 ways by which concrete manufacturers can reduce the carbon emissions related to their products:
- Switch the fuel source to a fuel generating less emissions.
This means moving from traditional fuels (e.g. coal) to lower-carbon fuels (e.g. renewable natural gas), waste fuels (e.g. non-recyclable plastics, non-recyclable tires, rail ties, etc.), and potentially even carbon-neutral fuels.
- Replace some cement content with mineral compounds.
A few substitutes to cement which can reduce the emissions in concrete are:
- Fly Ash (by-product of coal-burning power stations)
- Ground Granulated Blast-furnace Slag (GGBS) (by-product of the Iron and Steel Industry)
- Silica fume (by-product from the manufacture of silicon)
- Limestone fines.
- Install Carbon Capture and Storage technologies on-site
Innovation in carbon capture, utilization, and storage (CCUS) technologies is an exciting development in the concrete industry. Carbon capture theoretically makes it possible to capture up to 100% of the carbon emissions from cement manufacturing. These captured emissions can be stored safely underground, injected back into concrete to strengthen it, or used to make other products like synthetic aggregates or fuels.
Depending on the fuel used and the dosage of the additions, the carbon footprint of concrete can be reduced by up to nearly 70%.
Are all low carbon concretes equal?
In short, no.
While there’s been amazing progress in lowering carbon’s footprint, the industry still has big challenges.
Here’s some things to note around the technologies which limit their scalability today:
- Alternative fuels today can reduce emissions by a small amount and face several issues in being adopted globally such as high costs, limited range, etc.
- Cement replacements such as fly-ash and slag are finite. There isn’t enough slag and fly-ash in the world to apply it to all the concrete being produced.
- Cement replacements are reducing. Since these are by-products of other sectors (some of which are winding down globally) their availability is becoming constrained.
- Carbon Capture and Storage is an expensive technology that needs further development to be applied at scale.
Future Thought Leaders is a democratic space presenting the thoughts and opinions of rising Energy & Sustainability writers, their opinions do not necessarily represent those of illuminem. This article is also published on 2050 Materials.